中宏网天津12月3日电在制造业领域,许多企业面临着一系列棘手的问题,比如:客户对于产品的个性化需求不断增长,而传统生产方式难以满足;行业竞争日益激烈,而企业得效率和质量难以保证。
数字工厂,正是为了解决这些难题而生。卓朗科技以现代数字制造技术、虚拟仿真技术、数字化多环节协同等为支撑,助力数字工厂实现设备互联高效协同、精益生产、柔性自动化、安全自主等场景的全面数字化和智能化。
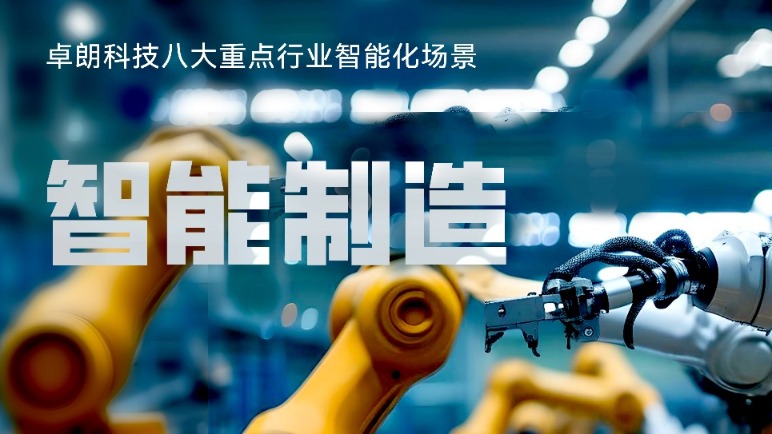
生产做优“虚拟现实+”内生能力
工业和信息化部等五部门联合发布的《虚拟现实与行业应用融合发展行动计划(2022-2026年)》指出,做优“虚拟现实+”内生能力,强化虚拟现实与5G、人工智能、大数据、云计算、区块链、数字孪生等新一代信息技术的深度融合,叠加“虚拟现实+”赋能能力;推进云、网、边、端协同能力体系建设。支持产业链上下游协同、面向特定场景、具备商用潜力的应用技术研发。
在卓朗天工数字孪生工厂解决方案中,数字孪生技术通过整合物理真实空间与虚拟空间各流程、各业务的有效数据,可实现工厂全生产要素在物理工厂、虚拟工厂、工厂服务系统间的迭代运行,最终使物理工厂不断迭代优化,让工厂生产和管控达到最优的一种工厂运行新模式。
以生产线场景为例,卓朗天工工厂3D数字孪生可视化及数采系统实现对工厂生产运营以及产线设备、设备运行数据的目视化管理。利用全产线3D建模,将设备、生产线监控、T/Time、异常波动预警等映射到模型,还原产线运行场景,实时展示产线状态,指导管理人员进行生产效率优化、生产质量提高和生产成本降低等改善活动。
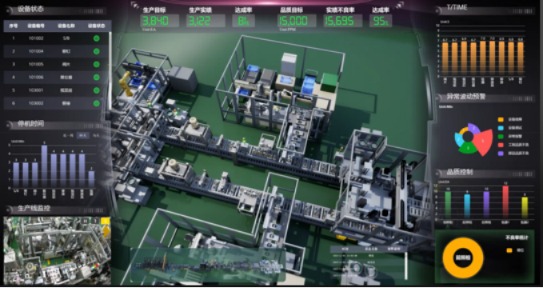
物流赋能生产流程柔性化
随着数字化产线快速发展,AGV(Automated Guided Vehicle,自动导引车)作为一种自动导引车辆,以其高效、精准的特点,广泛应用于产线物流环节。
AGV小车可以跨流程、跨产线、跨区域运输物料、半成品和产品,实现生产流程柔性化,在自动化物流系统中充分体现其自动性和柔性化,实现高效、经济、灵活的无人化生产。
以重装焊材车间物流场景为例,卓朗天工智能配送AGV小车项目方案可根据不同焊材、装焊工位进行选择配送路线,实现自动上下料及来回运输工作,自动充电功能可让设备24小时连续运转工作,大大提高了工作效率。
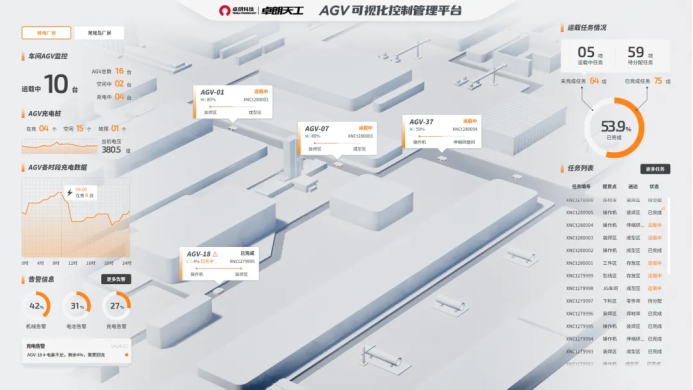
实训夯实安全生产防线
一名产线员工,入职后要经历几级安全生产培训才能合格上岗?从入厂培训到部门培训再到班组培训,至少三级!如果全部培训均以线下的形式进行,无疑企业培训压力将大幅提升。
以实训场景为例,卓朗昆仑云·机械加工安全实训平台通过虚拟仿真技术让员工培训不再单纯依靠纸质教材、笔试考试,而是通过线上、线下相组合的形式完成安全生产实训,微小的改变渗透到培训的各个环节,见缝插针地降低了成本,提高了人才标准化的效率,夯实“安全生产培训”的防线。
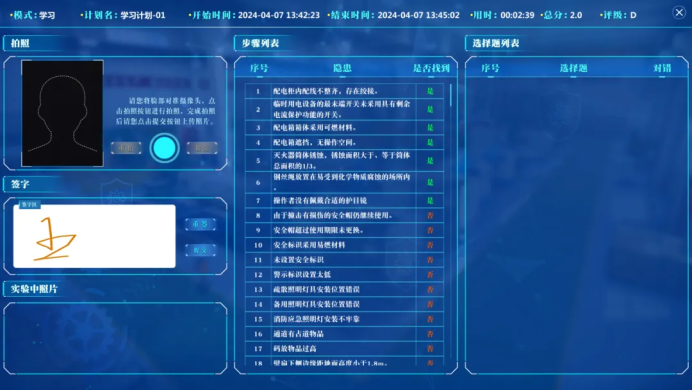
目前,卓朗昆仑云·机械加工安全实训平台深入挖掘机械设备、电工电气等多方面安全实训内容,梳理出200+源于生产一线、完全还原企业真实工业生产场景的安全隐患点,覆盖了20多种典型生产设备。平台适用于机械制造业,还涵盖高危行业、化工行业等多个涉及“安全”的领域。
卓朗科技将持续聚焦智慧工厂,深入运用物联网、大数据、云计算、人工智能等先进技术,对工厂内的人、机、料、法、环等要素进行全面感知、分析、优化和协同,实现从“制造”到“智造”,助力建设更多可持续发展、可广泛复制的多行业、多领域样板数字化工厂。(中宏网特约作者王敏报道图文/由主办方提供)
(文章来源:中宏网)